Um besser zu verstehen, wie ein modernes Lithium-Batteriesystem funktioniert und welche Hürden es bei einem Eigenbau zu nehmen gilt, wurde ein Eigenbau in Angriff genommen. Die Kapazität wurde mit 19,2 kWh so groß gewählt, dass man auch einen Sommertag ohne Nachladen bestreiten können sollte. Zudem konnten preiswertere Zellen aus dem PV-Bereich verwendet werden, in diesem Fall 60 Stück mit jeweils 100Ah, von denen jeweils zwei parallel geschaltet wurden. Der maximale Entladestrom von ca. 140 A liegt somit lediglich bei 0,7C, der typische Wert unter 0,5C.
Zunächst wurde erwogen, als einfache und preiswerte Lösung die stabile Metallkonstruktion des Anhängers als Behältnis zu verwenden und die Zellen direkt auf die Ladefläche zu montieren, einen umlaufenden Holzkasten aus Siebdruckplatten zu bauen und die Zellen gegen Ausbauchen mit passenden Druckplatten zu sichern. Zur vertikalen Befestigung hätte man recht unkompliziert stabile Streben mit den Bordwänden verschrauben können. Das hätte ungefähr so ausgesehen:
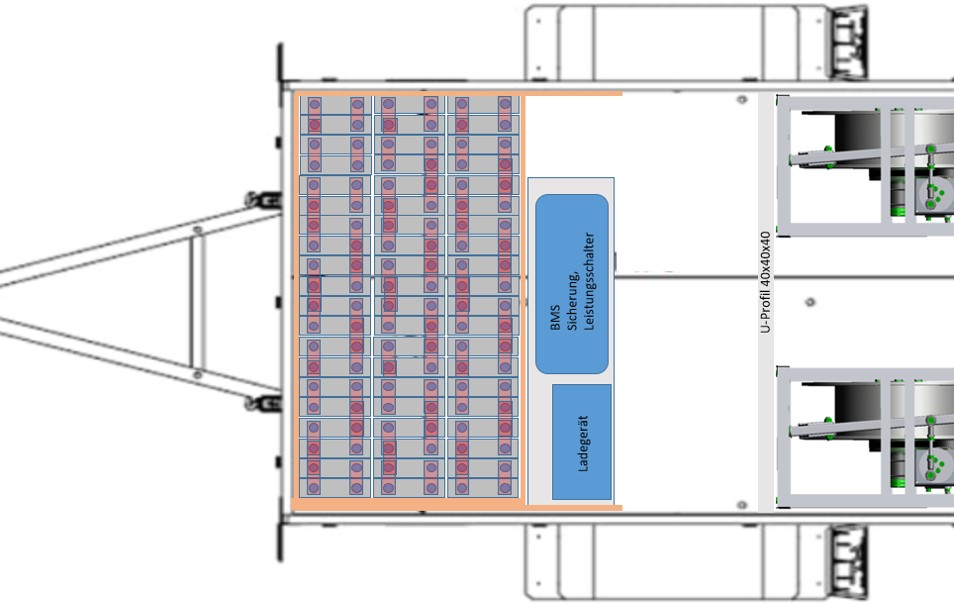
Da es sich allerdings nur um eine temporäre Lösung handeln und die Batterie später auf einem anderen Gefährt montiert werden sollte, wurden stattdessen zwei für diesen Zellentyp verfügbare Metalltröge verwendet, die mit jeweils 30 Zellen bestückt werden konnten. Da solche Tröge in der Regel mit hohem Aufwand hergestellte Einzelanfertigungen oder Kleinserien sind, tragen sie nicht unerheblich zum Gesamtpreis einer Batterie bei. Alternativ war auch überlegt worden, Flight Cases aus dem PA-Bereich zu verwenden und mit Platten zu verstärken. Skizziert ergibt sich folgendes Bild:
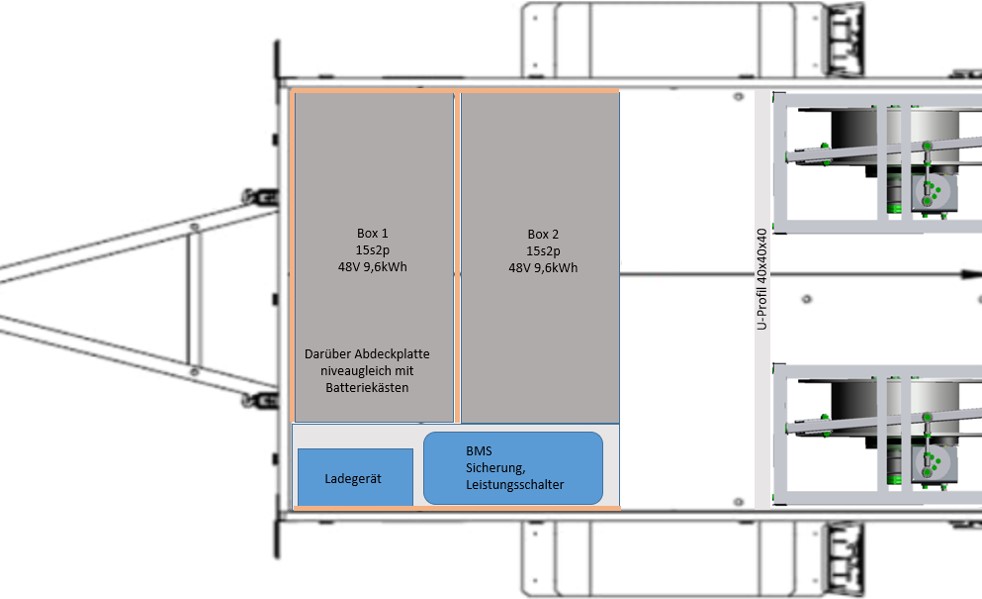
Mit diesen Festlegungen und einer Skizze der geplanten Zellenanordnung konnte es nun ans Auspacken der Zellen und das Bestücken der Tröge gehen. Ab jetzt war erhöhte Aufmerksamkeit angesagt wegen möglicher Kurzschlussgefahr. Etwas verwirrend war zunächst die Farbgebung der Pole: Schwarz für den Pluspol und Hell für den Minuspol – vor dem Platzieren der ersten Zelle wurde lieber zweimal nachgemessen und einmal telefoniert.
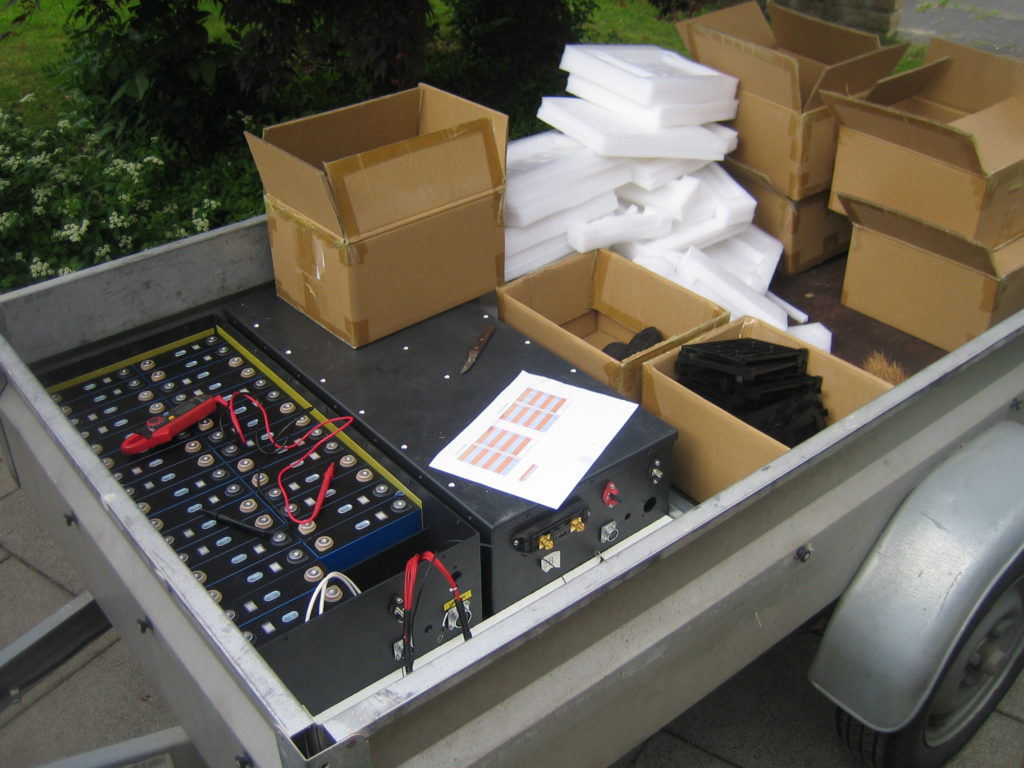
Die kurzen Aluminiumgewinde in den Zellenpolen wirkten nicht sehr stabil. Daher wurden Stehbolzen eingeschraubt, um mehr Stabilität zu erhalten und das Problem zu umgehen, dass man pol-spezifische Gewindeschraubenlängen benötigt, die mit der Zahl der Zellenverbinder, Sensorscheiben usw. variieren würde. Das ist kaum ein Zusatzaufwand, erleichtert die spätere Montage sehr und verringert auch das Kurzschlußrisiko bei der Montage. Allerdings wurde zunächst darauf verzichtet die Bolzen mit hochfestem Gewindekleber einzukleben, was sich später rächte – alles musste nocheinmal demontiert und mit Anwendung von Kleber neu verschraubt werden.
Bis dahin war die Gefahr eines versehentlichen Kurzschlusses eher gering. Es wurde lediglich darauf geachtet, dass keine längeren metallischen Teile in die Tröge gelangen konnten. Das änderte sich mit dem Auflegen und Festschrauben der Zellenverbinder: ab nun konnten auch kleinere Metallteile zu Kurzschlüssen und sehr hohen Strömen mit gefährlichen Lichtbögen usw. führen. Daher wurden alle zu verwendenden Werkzeuge (konkret: ein Steckschlüssel, ein Ringschlüssel und ein Inbusschlüssel) soweit wie möglich mit Isolierband umwickelt, bevor Verbinder für Verbinder aufgelegt und an den relevanten Polen die Spannungs-Sensoren und gelegentlich auch Temperatursensoren festgeschraubt wurde. Fertiggestellte Stromschienen wurden mit breitem Isolierband abgedeckt. Dann wurden die Außenanschlüsse über eine 300A-Schmelzsicherung mit der Batterie verbunden. Zuletzt wurden die Querverbinder zwischen den Akku-Reihen aufgeschraubt: nun war der Trog „scharf“ und über die Sicherung gegen Kurzschlüsse von Außen geschützt. Allerdings stellte erst das Auflegen der Deckel auch einen Schutz vor internen Kurzschlüssen und damit ein beruhigendes Gefühl her.
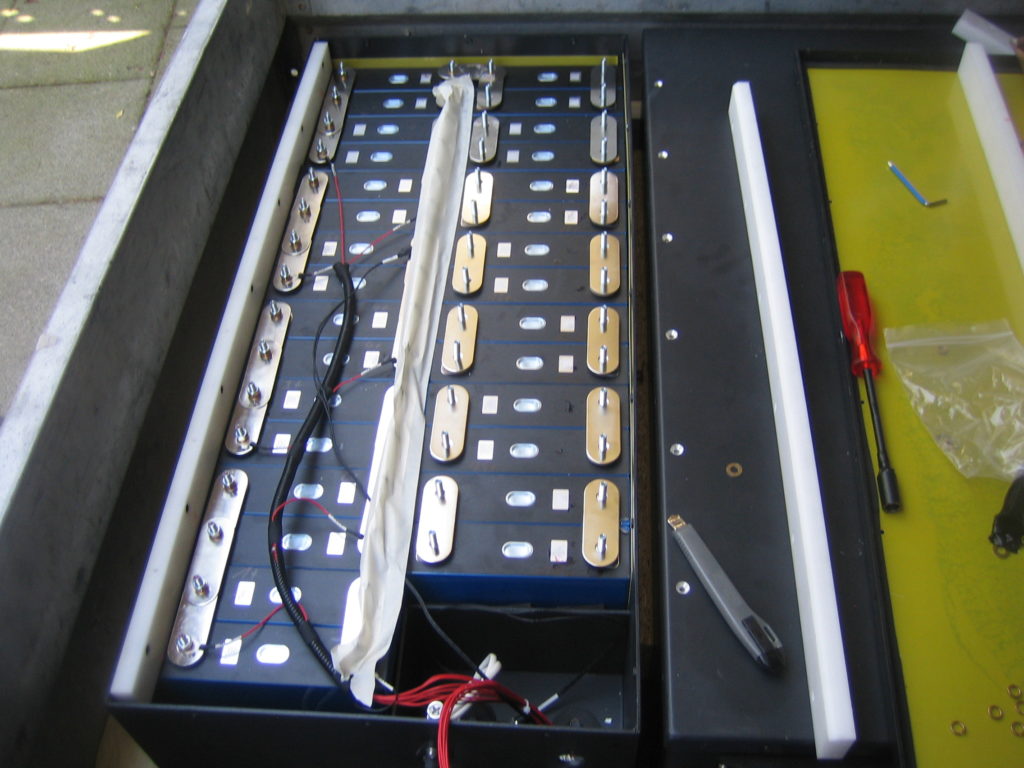
Mit den Zellen wurde auch ein Batterie-Managementsystem (BMS) mit Kabelbaum, Leistungsschaltern, Sicherung, Shunt, Alarmsummer und Display beschafft. Das gezeigte Pre-Charge-Relais zur Vermeidung hoher Einschaltströme bei entladenen Kondensatoren ist für die Elowin nicht erforderlich, da der Modul-Controller diese Funktion mit erledigt. Auch das gezeigte Last-Relais wäre bei entsprechender Verschaltung entbehrlich, da die Modul-Controller über eigene Lastrelais verfügen, ebenso wie das BMS-Relais. Der Vorteil dieser Relais liegt allerdings darin, dass das BMS alle Komponenten und auch sich selbst vollständig von den Akkus trennen kann. So kann eine drohende Tiefentladung, zB. bei monatelangem Stillstand in der Winterpause, abgewendet werden.
Der fertig konfektionierte und beschriftete (!) Kabelbaum war sehr hilfreich, um die 31 Spannungspegel (Minuspol sowie 30 Zellen-Pluspole) zum BMS zu führen und die übrigen Komponenten zu verdrahten.
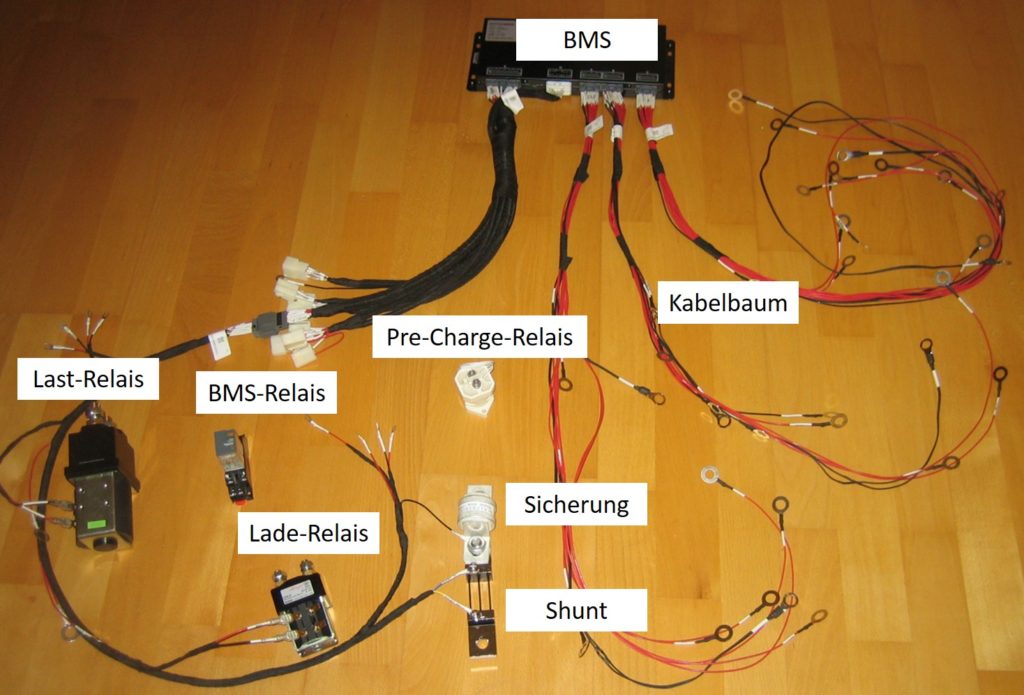
Allerdings passten die Kabellängen der Spannngssensoren nicht zur gewählten Zellenanordnung. Glücklicherweise waren in den Trögen bereits passende Kabelbäume vorinstalliert. Sie mussten „nur“ noch über passende Steckverbinder an das BMS geführt werden. Das erforderte hohe Konzentration, um einerseits saubere, belastbare Lötverbindungen zu erhalten und andererseits sicher zu sein, dass kein Fehler unterläuft, den das teure BMS vermutlich mit einem sofortigen Exitus quittieren würde.
Also wurde vorher ein detaillierter Kabelplan erstellt und nach dem Lötvorgang jede einzelne Verbindung durchgemessen. Dann wurden die Stecker verschraubt und testweise an den Trögen angeschlossen. Nun konnte final nachgemessen werden, dass an den BMS-Steckern überall die richtige Spannung anlag. Doppel hält besser. Danach wurden die Stecker nochmals aufgeschraubt, alle bereits vor dem Löten aufgeschobenen Schrumpfschlauchstücke über die Kontakte geschoben und festgeschrumpft. Insgesamt eine nervtötende und zeitraubende Angelegenheit, aber lohnend, da der geplante spätere Umbau der Batterie auf ein anderes Gefährt damit sehr einfach wird.
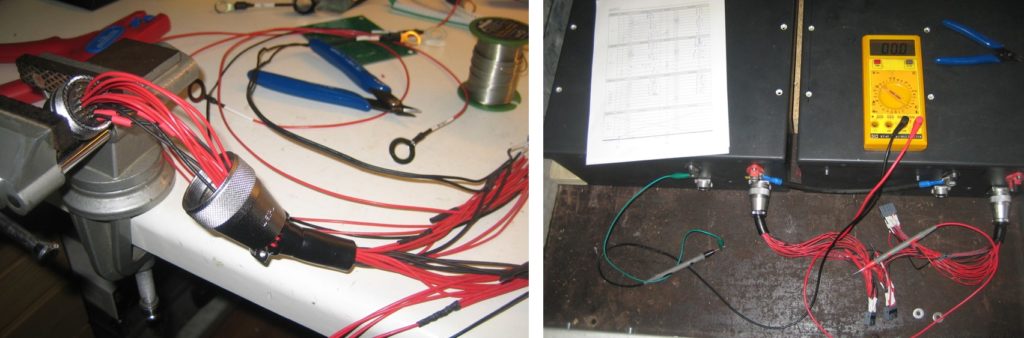
Es folgten Aufbau und Verkabelung des BMS und des Ladegeräts. Die einzelnen Komponenten wurde auf einem Holzbrett so verschraubt, dass später alle Verbindungen von oben bequem zugänglich sein würden. Das Brett wurde so bemessen, dass es exakt zwischen Tröge und Bordwand eingeschoben werden konnte und damit die Tröge seitlich fixiert.
Da das Gesamtsystem einigermaßen komplex und die Dokumentation teilweise lückenhaft war, fand zuerst ein Probelauf auf dem Arbeitstisch statt. Die Versorgung des BMS, das wie die meisten Systeme eine Versorgungsspannung zwischen 10 und 30 Volt erfordert, erfolgt durch einen DC-Wandler von Meanwell, der sich vielfach bewährt hat und einer der wenigen preiswerten Wandler ist, die Eingangsspannungen über 100 Volt akzeptieren.
So konnten Wissenslücken geschlossen werden. Auch konnte das System auf diese Weise mit PC und CAN-Bus-Adapter an die Batterie angepasst sowie Ein- und Ausschalter, Summer, das Display usw. schonmal bequem getestet werden.
Es fehlte noch eine Bedieneinheit für das Display und die Schalter, die abgesetzt von der Batterie und demontierbar über ein Kabel verbunden werden sollte. Dazu wurde ein handelsübliches Elektronikgehäuse verwendet.
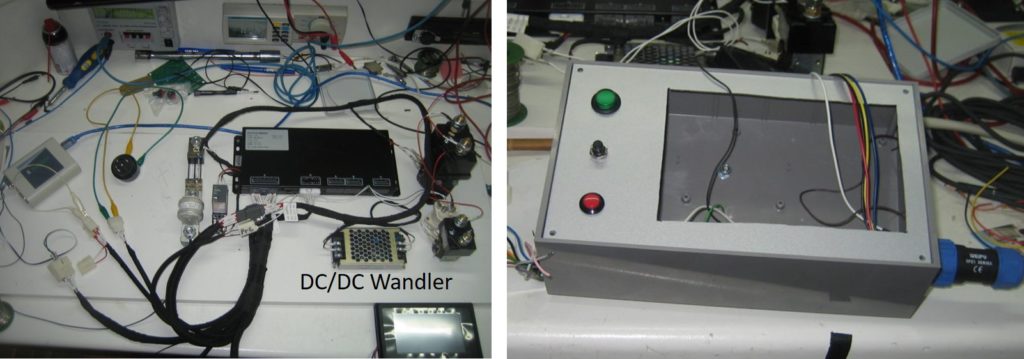
Nachdem im Keller alles zufriedenstellend funktionierte, verlief der Umzug der Komponenten auf den Anhänger ohne Probleme. Dort wurden die fehlenden Anschlüsse ergänzt, insbesondere die Starkstrom-Verbindungen zwischen Batterie, Windenmodulen und Ladegerät, die überwiegend mit 10mm-Rohrkabelschuhen ausgeführt wurden. Nach einem Funktionstest konnte dann die schützende Abdeckplatte montiert werden.
Die Aussparung seitlich links dient nicht nur dem Herausführen der Kabel für das Steuergerät und den 230V-Ladestecker, sondern auch der besseren Belüftung des Ladegeräts. Das Steuergerät kann mit einem Haken an eine der Bordwände gehängt und so auch bei montiertem Spriegel abgelesen werden, zB. beim Ladevorgang in der Garage.
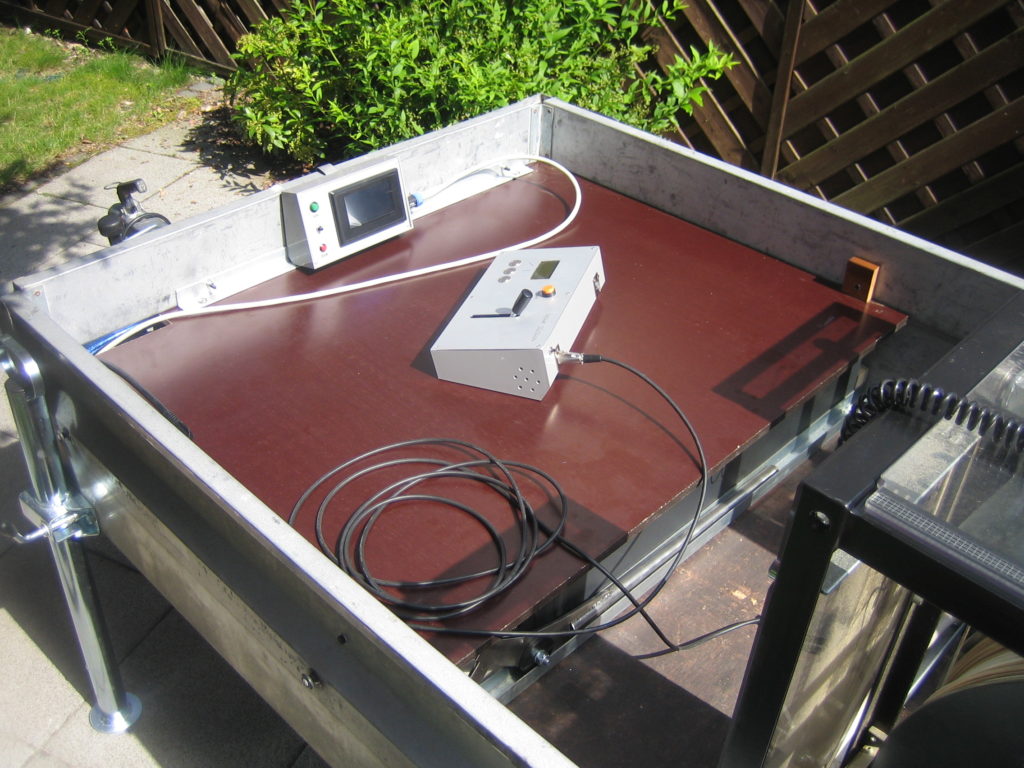